Technology introduction
Spheroidizing technology
Spherical nickel hydroxide is the product our company focuses on. It has been successfully used heavily as a cathode active material in alkaline rechargeable batteries, and we have received very high praise for it from major battery manufacturers both domestically and abroad.
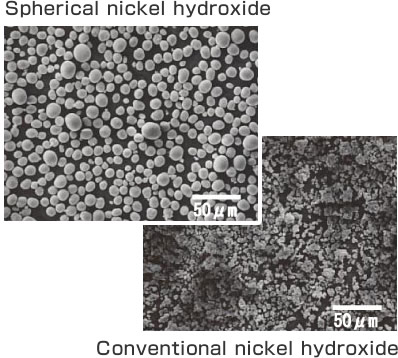
Photo of spherical product
Our company's technology can successfully produce high-density nickel hydroxide in a roughly spherical shape as shown in the photo. Nickel hydroxide produced using traditional methods produces countless crystal nuclei and interferes with the crystal formation process, and it results in creating porous particles. Furthermore, the particles become shapeless, and when used in the manufacture of batteries, etc. the volume energy density is low.
The manufacturing method for spherical nickel hydroxide is different from traditional methods, adding an addition agent to the reaction vessel to control the crystal formation reaction, allowing the creation of roughly spherical articles with small pore volume. By precisely controlling chemical and physical conditions in the crystallization process it is possible to obtain particles with any particle diameter, specific surface area, crystalline nature, and bulk density.
Superior fillability
As shown in the figure, when amorphous particles are filled there are many gaps, leading to a lower filling density. However, when filling with spherical particles, wasteful gaps are prevented and liquidity is superior, leading to drastic increase of the filling density. By making the particles spherical, the bulk density is increased, creating particles with high fillability and liquidity and also improving the handling, creating potential benefits in a variety of compounds.
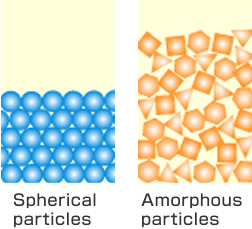
Different chemical element solid solution technology
By mixing multiple elements at the atomic level you can anticipate the creation of new high-performance compounds.
These can be applied to battery materials, catalysts, pigments, and more.
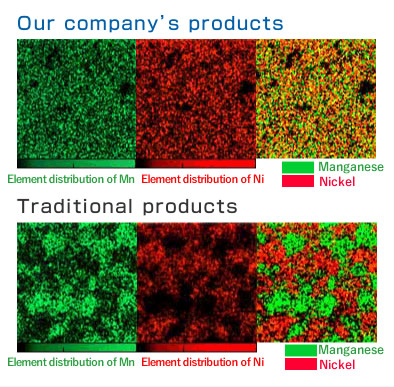
Distribution of chemical elements (example of Manganese and Nickel)
When mixing multiple types of powders together to create a composite oxide it is difficult to obtain a perfect mixture due to some parts easily becoming ununiform, etc. Using our company's technology enables the creation of precursors mixed uniformly at the chemical element level by controlling a variety of reaction conditions, and by firing these precursors we can obtain a composite oxide.
In addition to Ni-Mn we have also succeeded with 2-component types such as Ni-Co and Co-Mn as well as solid solution formations with 3 or more chemical elements.
Coating technology
By applying a coating process to the powder surface it is possible to effectively utilize the characteristics of that material with the lowest amount possible, reducing costs.
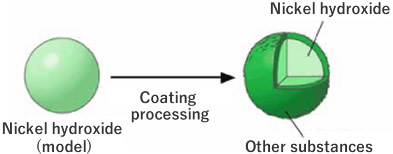
Example of coating onto Nickel hydroxide
Cobalt coating onto Nickel hydroxide is an example of the application of surface treatment technology at our company.
Features of coat products
This is a surface coating technology where the surface of a fine powder is coated with a different substance to create a composite material changing the surface characteristics to achieve higher performance and functionality. This technology improves the advantages of both the base material substance and the coating substance via a synergistic effect without being influenced by the type of base material, while also having the potential to offset the disadvantages of both substances. It enables the new creation of surface possessing more optimum performance and functionality and is able to control the various characteristics of the substances.
The development of new materials via coatings enables a reduction in additive substances and a reduced development time compared to developing new materials in the traditional way, allowing for an efficient increase in added value of raw materials. Furthermore, we firmly believe that the coating technology can play an active role in a variety of industrial fields as a special technology such as being useful in the development of fields to meet the needs of modern society, namely small size and weight, saving of resources, and reduction of costs.
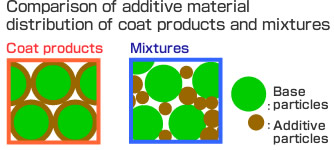
Fine powder production technology
By making the fine powder minute you can fine-tune the powder to possess special characteristics and achieve the discovery of new functional materials.
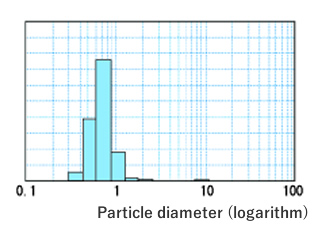
As characteristics of microparticles of sub-micron size and lower, you can discover functionality which differs from micron order powders not only in terms of the small particle diameter but also physical characteristics like specific surface area and surface roughness, as well as optical characteristics, magnetic characteristics, and chemical characteristics. Examples of applications of microparticles include the following types of items.
Application examples
- 1. Pigment
- The smaller the particle diameter is, the stronger the coloring power, which is the principle characteristic of pigment, becomes.
- 2. Fine ceramics
- The sinterability of fine ceramics is inversely proportional to the particle diameter, so a smaller particle diameter is deemed desirable. Improving sinterability can increase productivity by reducing sintering temperatures and can increase performance of IC circuit boards, sensors, engines, and other electronic and machine materials.
- 3. Catalysts
- The larger the specific surface area of the active component is, the more catalyst activity improves. A smaller particle diameter increases the number of active sites per unit weight, enabling the reduction of amount of catalyst used.